Nissan’s Bold Strategy: Keeping All Five Domestic Plants Operational Amid Restructuring
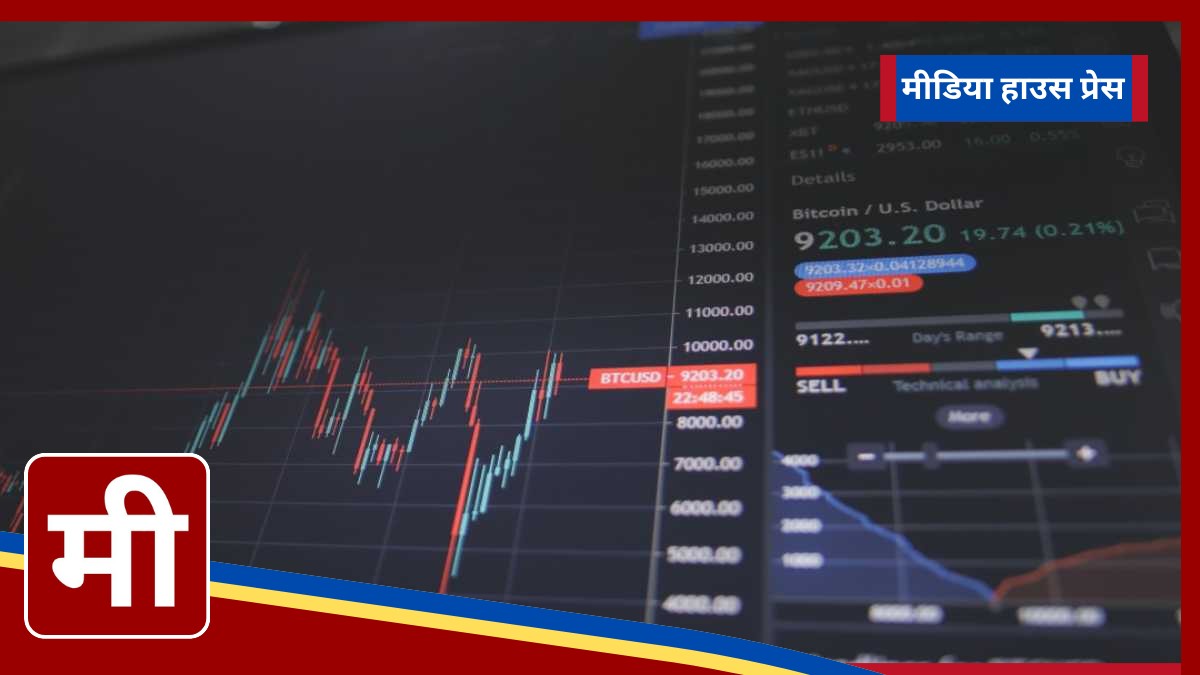
A Defining Moment for Nissan’s Future
In a significant move that reaffirms its long-term commitment to domestic manufacturing, Nissan Motor Co Ltd (7201) has announced its decision to keep all five of its vehicle assembly plants in Japan operational under a newly developed restructuring plan. This decision, reported by Kyodo News, comes as the automotive giant navigates an increasingly complex industry landscape marked by global supply chain disruptions, evolving consumer preferences, and the rise of electric vehicles (EVs). By maintaining its existing production network, Nissan signals a strategic shift that prioritizes manufacturing resilience, employment stability, and technological innovation.
The Strategic Shift in Nissan’s Domestic Operations
Nissan’s restructuring plan is not just about maintaining the status quo but about adapting to a rapidly evolving global automotive industry. As competition intensifies among automakers, Nissan’s approach underscores the importance of retaining a strong domestic production base while refining its operations for efficiency and cost-effectiveness.
In recent years, many global car manufacturers have reevaluated their production strategies, opting for cost-cutting measures such as plant closures, layoffs, or offshoring production to lower-cost regions. However, Nissan’s decision to keep all five plants in operation challenges this trend. Instead of scaling down, the company is focused on strengthening its manufacturing ecosystem in Japan, reinforcing its supply chain, and ensuring it remains a key player in the evolving automotive market.
Economic and Workforce Considerations
Japan’s automotive industry is a crucial pillar of its economy, employing millions and contributing significantly to GDP. Nissan’s move to sustain its domestic plants reassures its workforce and the local communities that rely on these manufacturing hubs. It also prevents potential economic disruptions that could arise from plant closures, including job losses and declining regional economic activity.
In an era where automation and artificial intelligence (AI) are transforming production processes, Nissan’s strategy appears to balance innovation with employment retention. By keeping its plants operational, Nissan can ensure a smoother transition toward next-generation manufacturing without drastic workforce reductions.
Commitment to Innovation and Sustainability
A key driver of Nissan’s decision to keep its domestic plants running is its ambitious push toward innovation and sustainability. As the automotive industry shifts toward electrification and carbon neutrality, Nissan aims to position itself as a leader in the production of EVs, hybrid models, and cutting-edge vehicle technology.
Japan’s government has been actively promoting green energy initiatives and electric vehicle adoption, and Nissan’s domestic plants will play a crucial role in advancing this agenda. By investing in new technologies at these plants, Nissan ensures that its Japanese manufacturing sites remain competitive and contribute to the global shift toward sustainable mobility.
Electrification and Next-Generation Vehicles
Nissan has been at the forefront of electric vehicle innovation with models like the Nissan LEAF, one of the world’s best-selling electric cars. The company’s continued investment in its Japanese manufacturing plants suggests that these facilities will be key hubs for the production of next-generation EVs and hybrid vehicles.
This move is aligned with Nissan’s long-term strategy, which includes a major push toward solid-state battery technology, improved charging infrastructure, and expanded EV offerings. By keeping its plants operational, Nissan secures the ability to rapidly scale production and respond to surging EV demand worldwide.
Strengthening Supply Chain Stability
One of the major challenges facing the global automotive industry is supply chain instability. From semiconductor shortages to pandemic-induced disruptions, automakers worldwide have been forced to rethink their production strategies. By keeping its domestic assembly plants operational, Nissan ensures a more controlled and resilient supply chain.
By maintaining a robust domestic production network, Nissan can better manage parts procurement, streamline logistics, and mitigate risks associated with over-reliance on international suppliers. Additionally, Japan’s reputation for high-quality manufacturing ensures that vehicles produced in Nissan’s domestic plants meet the highest standards of reliability and innovation.
Nissan’s Global Competitiveness: A Strategic Advantage
Nissan’s decision to sustain its Japanese production network also reflects its ambition to remain competitive in the global automotive sector. The industry is undergoing profound transformations, with emerging players in China and established competitors in the U.S. and Europe investing heavily in autonomous driving technology, connected vehicles, and EV infrastructure.
By keeping all five of its domestic plants operational, Nissan reinforces its reputation as an automotive powerhouse that values long-term growth over short-term cost-cutting measures. This move is expected to yield significant advantages:
- Faster Adaptation to Market Trends: Having a stable production base allows Nissan to quickly adjust to shifts in consumer demand, particularly as the EV market continues to evolve.
- Higher Manufacturing Quality: Japan has long been recognized for its precision engineering and rigorous quality control. By keeping production local, Nissan ensures that its vehicles maintain these high standards.
- Enhanced Research & Development (R&D) Synergy: Retaining domestic manufacturing facilities allows Nissan’s R&D teams to work closely with production units, accelerating the integration of new automotive technologies.
Challenges and Future Prospects
While Nissan’s strategy presents several advantages, it does not come without challenges. Maintaining all five plants means that Nissan must continuously invest in upgrading facilities, enhancing automation, and optimizing production costs to remain competitive with manufacturers that have shifted production to lower-cost countries.
Additionally, raw material costs, energy expenses, and labor wages in Japan are relatively high, which could put pressure on Nissan’s profit margins. To counter this, the company is expected to invest heavily in advanced manufacturing technologies, AI-driven automation, and lean production techniques to maintain cost efficiency while improving productivity.